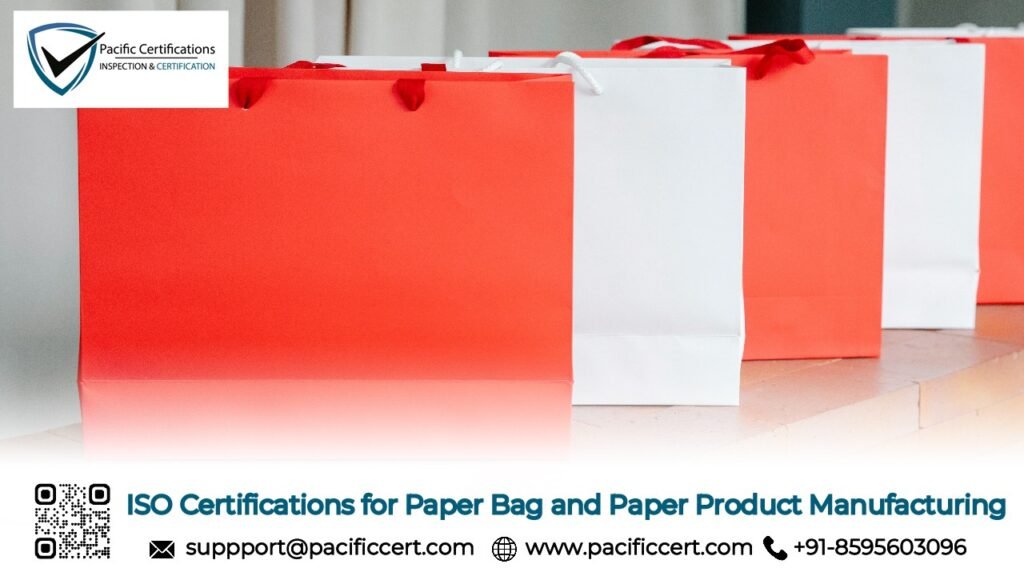
ISO Certifications for Paper Bag and Paper Product Manufacturing, Requirements and Benefits
The demand for sustainable paper bags and paper products is surging globally, driven by environmental concerns and consumer preference for eco-friendly alternatives. Achieving ISO certifications is an excellent way for manufacturers to showcase their commitment to quality and environmental sustainability.
ISO standards are internationally recognized frameworks designed to ensure products, services, and systems meet quality, safety, and efficiency benchmarks. In the paper bag and paper product manufacturing industry, these standards address key aspects like environmental impact, product quality, worker safety, and supply chain management.

For manufacturers, obtaining ISO certification is a testament to their dedication to adhering to global best practices. With the paper products sector leaning heavily toward sustainability, ISO standards provide a structured approach to align business operations with environmental and regulatory expectations.
If you’re seeking ISO certification for your paper bag and paper product manufacturing business, we’re here to assist. Reach us at support@pacificcert.com or call +91-8595603096 to begin your certification journey.
Applicable ISO Standards for Paper Bag and Paper Product Manufacturing
Numerous ISO standards apply to the paper bag and paper product manufacturing industry. Here are the most relevant ones:
- ISO 9001: Quality Management Systems (QMS): ISO 9001 ensures manufacturers maintain consistent product quality. It emphasizes customer satisfaction, continual improvement, and adherence to regulatory requirements.
- ISO 14001: Environmental Management Systems (EMS): ISO 14001 helps organizations minimize their environmental footprint. This standard is vital for paper manufacturers aiming to reduce waste, optimize energy use, and comply with environmental regulations.
- ISO 45001: Occupational Health and Safety Management: This standard focuses on creating a safe working environment for employees. It’s particularly relevant for paper product manufacturers, as production processes often involve machinery and hazardous materials.
- ISO 22000: Food Safety Management Systems: For manufacturers producing paper bags for food packaging, ISO 22000 ensures products are safe for food contact, addressing hygiene and contamination prevention.
- ISO 22301: Business Continuity Management Systems: ISO 22301 prepares manufacturers to handle disruptions like supply chain issues or machinery downtime, ensuring continued operations and customer satisfaction.
- ISO 50001: Energy Management Systems: This standard supports energy efficiency in manufacturing processes, reducing operational costs and environmental impact.
- ISO 20400: Sustainable Procurement: ISO 20400 guides organizations on integrating sustainability into procurement processes, ensuring raw materials and suppliers align with ethical and environmental standards.
Click here to find out more applicable standards to your industry
At Pacific Certifications, we specialize in providing auditing and certification services for businesses seeking ISO compliance. We work with paper bag and paper product manufacturers to ensure their operations meet the rigorous demands of ISO standards. With our experienced auditors, organizations can confidently navigate the certification process and demonstrate their commitment to quality and sustainability.
Our impartial and professional approach ensures that manufacturers receive certifications reflecting genuine compliance with international standards. By choosing Pacific Certifications, you gain a trusted partner dedicated to maintaining the integrity of your business processes.
Take the first step toward ISO certification for your paper product manufacturing business today. Email us at support@pacificcert.com or call +91-8595603096 for support.
Requirements of ISO Certifications for Paper Bag and Paper Product Manufacturing
ISO standards provide detailed frameworks tailored to specific operational areas of paper bag and paper product manufacturing. Below is a breakdown of the key requirements for each relevant ISO standard:

ISO 9001: Quality Management Systems (QMS)
- Quality Policy and Objectives: Develop a documented quality policy reflecting the company’s commitment to customer satisfaction and continuous improvement.
- Process-Based Approach: Identify, manage, and optimize all processes affecting product quality, from procurement to delivery.
- Customer Focus: Prioritize customer requirements, monitor satisfaction, and implement feedback systems.
- Documented Information: Maintain records of quality procedures, performance metrics, and corrective actions.
- Risk-Based Thinking: Identify potential risks and opportunities in processes, ensuring consistent product quality and compliance.
- Performance Evaluation: Conduct internal audits and management reviews to monitor quality management system (QMS) effectiveness.
ISO 14001: Environmental Management Systems (EMS)
- Environmental Policy: Establish a formal policy addressing the organization’s commitment to environmental protection and sustainability.
- Environmental Aspects and Impacts: Identify and evaluate the environmental impact of production activities, such as waste, emissions, and resource use.
- Compliance Obligations: Meet applicable environmental laws, regulations, and other binding commitments.
- Objectives and Targets: Set measurable goals for reducing environmental impact, such as lowering energy consumption or minimizing waste.
- Operational Control: Implement procedures to manage significant environmental impacts, including waste management and pollution prevention.
- Monitoring and Measurement: Regularly assess environmental performance through audits and continuous monitoring.
ISO 45001: Occupational Health and Safety Management
- Health and Safety Policy: Develop a documented policy that outlines the organization’s commitment to ensuring a safe workplace.
- Hazard Identification and Risk Assessment: Identify potential hazards in manufacturing processes and evaluate associated risks to prevent accidents.
- Legal and Regulatory Compliance: Adhere to occupational health and safety laws and industry standards.
- Emergency Preparedness and Response: Establish plans for responding to emergencies, such as fire or machinery breakdowns.
- Employee Participation: Engage employees in safety initiatives, including reporting hazards and participating in risk management.
- Continuous Improvement: Monitor workplace safety performance and implement corrective actions to improve conditions.
ISO 22000: Food Safety Management Systems (For Food Packaging)
- Food Safety Policy: Define a food safety policy addressing the hygiene and safety of paper bags used for food packaging.
- Hazard Analysis and Critical Control Points (HACCP): Implement HACCP principles to identify and control potential contamination risks.
- Traceability System: Ensure traceability of raw materials and finished products to manage recalls if needed.
- Good Manufacturing Practices (GMP): Maintain high hygiene standards in facilities and processes to prevent contamination.
- Monitoring and Verification: Regularly evaluate the effectiveness of food safety controls and procedures.
ISO 50001: Energy Management Systems
- Energy Policy: Define a policy emphasizing energy efficiency and reduction of energy consumption in manufacturing.
- Energy Review and Baseline: Assess energy usage patterns, establish a baseline, and identify areas for improvement.
- Objectives and Targets: Set measurable energy efficiency goals, such as reducing electricity consumption by a specific percentage.
- Operational Controls: Implement measures to monitor and reduce energy waste during production.
- Monitoring and Reporting: Track energy performance regularly and report improvements to stakeholders.
ISO 20400: Sustainable Procurement
- Sustainability Policy: Outline the organization’s commitment to ethical sourcing and sustainable procurement practices.
- Supplier Evaluation: Assess suppliers based on environmental and ethical criteria, ensuring alignment with sustainability goals.
- Life Cycle Assessment: Evaluate the environmental impact of raw materials used in paper product manufacturing.
- Procurement Procedures: Establish guidelines to prioritize sustainable materials and suppliers.
- Monitoring and Reporting: Measure and report on the sustainability performance of procurement activities.
These requirements serve as a roadmap for paper bag and paper product manufacturers aiming to achieve ISO certification, improve operational efficiency, and align with global standards. Each standard addresses specific facets of manufacturing, ensuring a comprehensive approach to quality, safety, sustainability, and business continuity.
For reliable ISO certification services for paper bag and paper product manufacturing, contact Pacific Certifications. Email support@pacificcert.com or phone +91-8595603096 for assistance.
Benefits of ISO Certifications for Paper Bag and Paper Product Manufacturing
Obtaining ISO certifications offers numerous advantages for paper bag and paper product manufacturers:
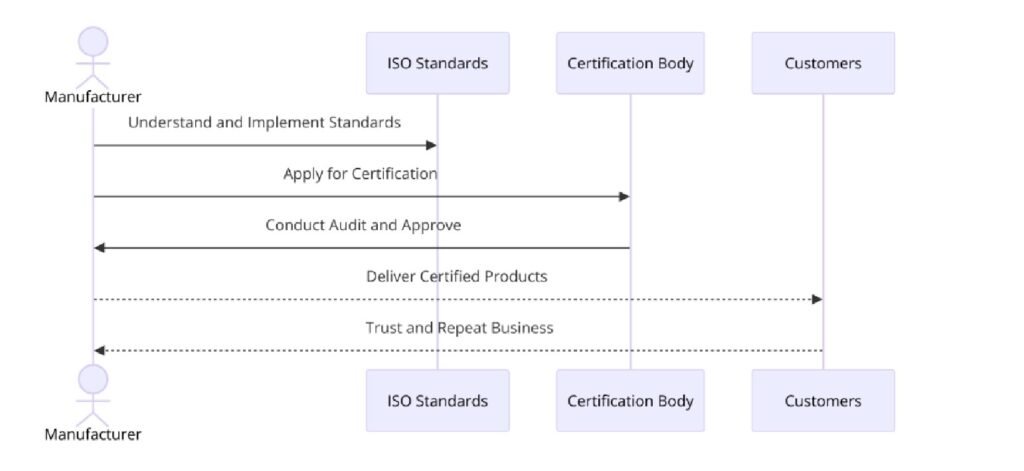
- Product Quality: ISO 9001 certification ensures products consistently meet customer expectations, boosting brand reputation and customer satisfaction.
- Environmental Performance: ISO 14001 helps manufacturers reduce waste, lower emissions, and conserve resources, showcasing their commitment to sustainability.
- Market Competitiveness: ISO-certified businesses stand out in the marketplace, often gaining access to larger contracts and environmentally conscious customers.
- Efficiency: Standards like ISO 50001 promote energy efficiency, while ISO 22301 ensures operational resilience, reducing costs and downtime.
- Regulatory Compliance: ISO certifications demonstrate adherence to local and international laws, minimizing the risk of legal issues and penalties.
- Employee Safety: With ISO 45001, manufacturers can create a safer workplace, reducing accidents and boosting morale.
- Stakeholder Relationships: ISO 20400 fosters sustainable procurement, strengthening relationships with eco-conscious suppliers and stakeholders.
The global market for paper bags and paper products is projected to grow significantly in 2024, driven by environmental regulations banning plastic bags and increasing consumer demand for biodegradable alternatives. According to recent research, businesses adopting sustainable practices, including ISO 14001 certification, are likely to dominate the market. This trend emphasizes the growing importance of aligning manufacturing practices with global sustainability goals.
Ready to elevate your business with ISO certifications? At Pacific Certifications, we’re here to help you achieve global recognition for your commitment to quality and sustainability.
Pacific Certifications is accredited by ABIS, in case you need support with ISO certification for your Paper Bag and Paper Product Manufacturing business, please contact us at suppport@pacificcert.com or +91-8595603096.
FAQs: ISO Certifications for Paper Bag and Paper Product Manufacturing
ISO certifications help manufacturers enhance product quality, improve sustainability, and comply with legal requirements, giving them a competitive edge in the market.
ISO 14001 is the primary standard for environmental management, focusing on reducing waste, emissions, and resource consumption.
ISO 9001 ensures consistent product quality, customer satisfaction, and continual improvement, strengthening brand reputation.
Yes, ISO 45001 focuses on occupational health and safety, helping manufacturers create safer working environments.
Sustainable procurement, guided by ISO 20400, ensures that raw materials and suppliers align with environmental and ethical standards, boosting stakeholder trust.
Pacific Certifications provides auditing and certification services to ensure your business meets ISO standards, reflecting your commitment to quality and sustainability.
Read More at: Blogs by Pacific Certifications
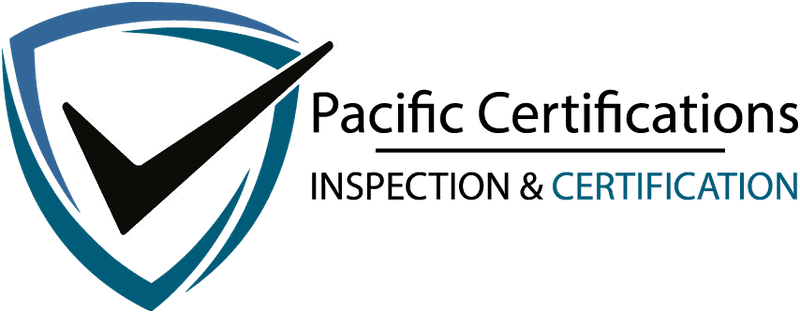